Quality control
Quality assurance is the most significant issue for companies handling foods.
In order to respond to increasingly demanded consumers’ security and safety, TDC has the Quality Assurance Division under the direct control of the president.
Quality assurance system
As a company that handles foods, securing the safety of the products handled is the most important priority. We have the Quality Assurance Department in place to ensure the safety of the products handled throughout the entire Group by assigning a person in charge of quality management with quality management personnel in each office.
President
Quality Assurance Department
- Quality Assurance Group (six people)
-
- Check and thoroughly announce food related regulations
- Scrutinizing of quality assurance documentation and specifications and database development for product information
- Employee training for quality assurance
- Quality Assurance Group (six people)
-
Local staff in China (x1)
Technical advisors (x3)- Confirm manufacturing and hygiene control
- Support quality management system, Support to prevent reoccurrence of problems
- Major qualifications of Quality Assurance staff
-
- ISO22000 Provisional Auditor
- ISO9001 Provisional Auditor
- HACCP Lead Instructor
- HACCP coordinator
- ASIAGAP coach
- PCQI lead instructor
- Food sanitation supervisor
- Food Labeling Adviser
- Delicatessen Manager
Internal training
Our individual employees associated with foods are also required to have knowledge of quality control and assurance. With an aim to raise the level of quality control ability across the company, we conduct quality management training and separate study sessions for employees as a part of the activity. In addition, for employees qualified for food safety we have a subsidy program for expenses to encourage the acquisition of qualifications.
Quality assurance training
Participation in factory (TDC Group factory)inspection training
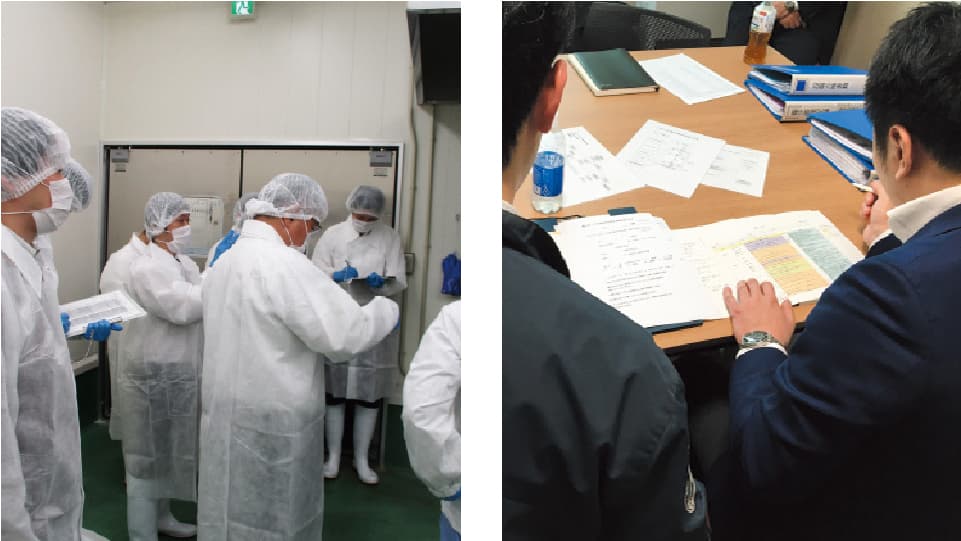
Training on quality control (classroom lecture)
Lecture contents (examples)
- What is HACCP?
- Quality control and problem preventigo by product
- How to pronare auality assurance documentation and some points
- What are the Food Labeling Act and Food Sanitation Act?
- Raw material information ard how to prepare food labeling (collective labeling)
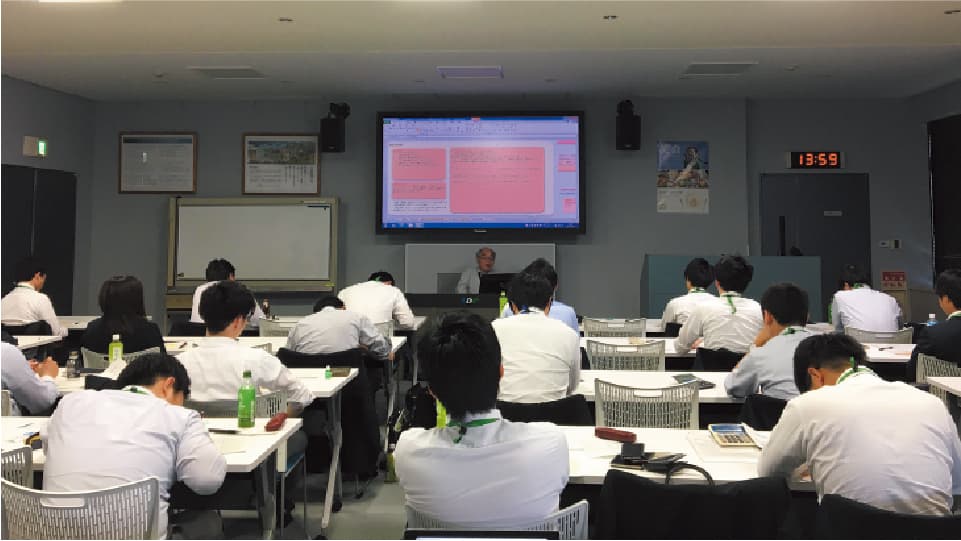
Qualifications encouraged by the company and the number qualified
- Food Labeling Adviser Total number of those qualified: 158
- Ready-made Meal Junior/ Senior/ Master Total number of those qualified: 182
Overseas factory audits
The Quality Assurance Group conducts factory audits of overseas suppliers, checks operations and the management documents at manufacturing sites, and provides advice and suggestions for improvements when necessary. In cases where on-site visits are not possible, audits are conducted remotely, and our local staff and supplier’s factory staff visit the production site and inform the auditor of the operational status and documentation management status, and the auditor conducts safety evaluations and offers advice and suggestions for improvements to the production site.Thus, we are working with our suppliers aiming to improve quality assurance.
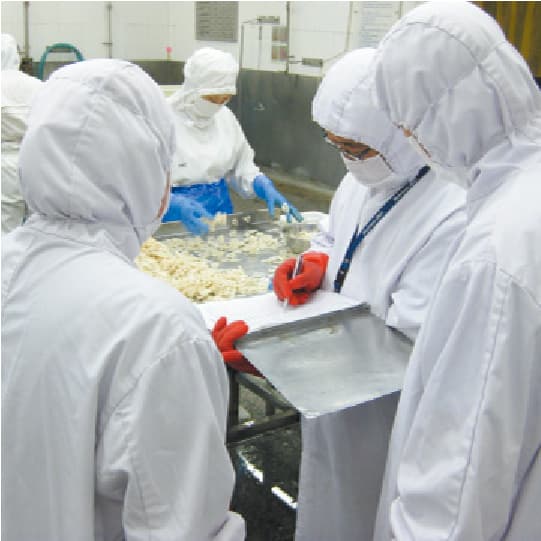
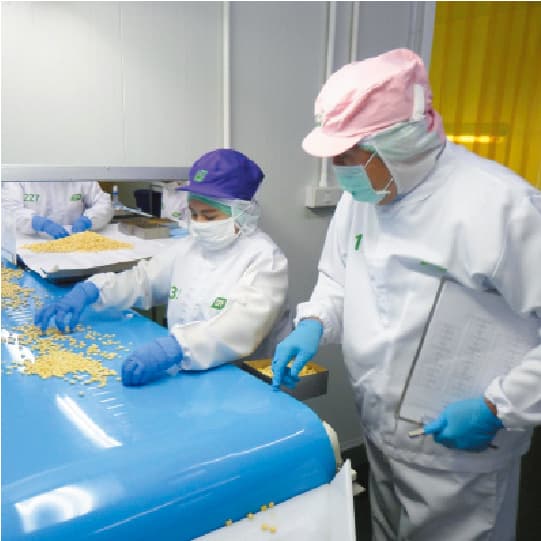
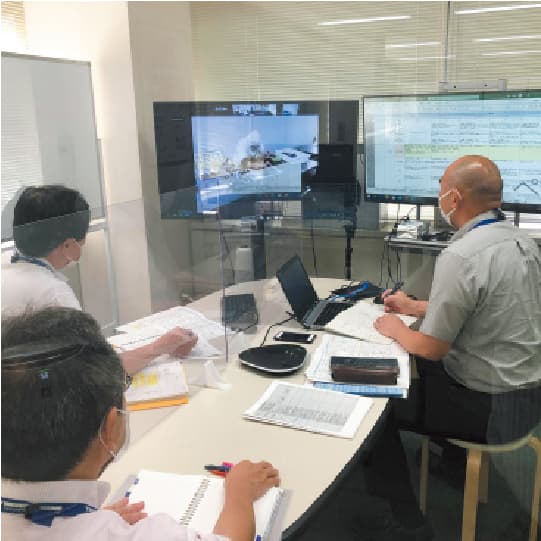
Check for product safety
The Quality Assurance Group checks information on our quality assurance documentation filled in and submitted by domestic and international suppliers. Our personnel check domestic food related regulations, the raw materials used, management standards and labels for the products, and save the product information as data to manage.
- Point1
-
- Collecting product information of our import products from affiliated companies
- Check of information given (allergens,microorganisms,raw materials used,additives,residual agricultural chemicals,processes,labeling,etc.)
- Point2
-
- Database development for checked information
- Allowing for prompt database search when a problem happens
- Preliminary check for overseas factory visit